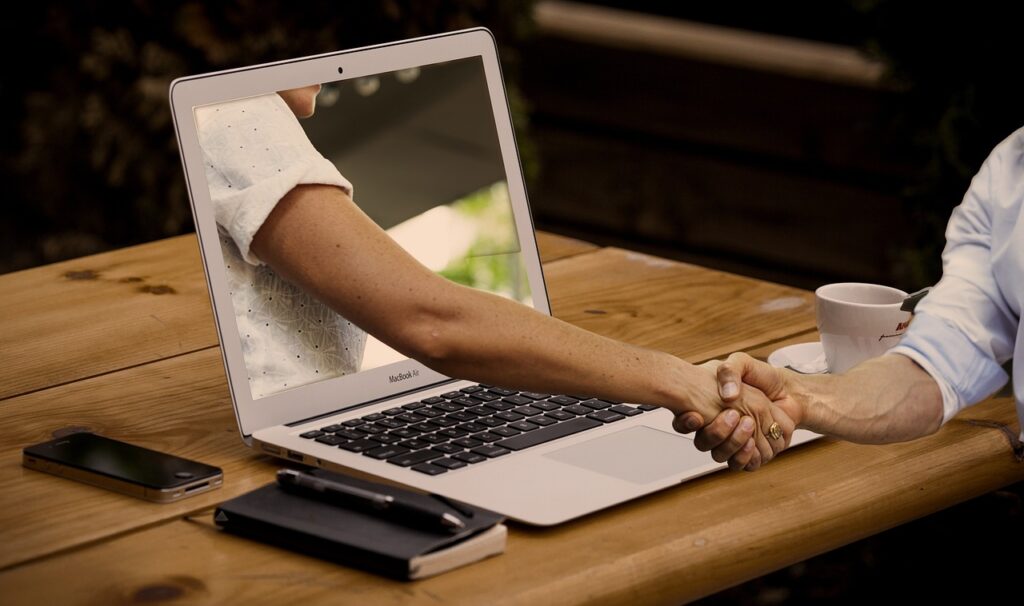
Image by Gerd Altmann from Pixabay
In Projekten geht es immer im Ziele, die erreicht werden sollen. Es erleichtert die Zusammenerarbeit in Organisationen, wenn schon eine Projektkultur Einzug gehalten hat, die die bisher in der Massenprpduktion vorherrschende Routinearbeit ergänzt, oder schon abgelöst hat. Dazu ist es weiterhin förderlich, wenn ein Projektleitbild zu etablieren und zu leben, das oft an das Agile Manifest erinnert. Das wiederum ist nicht verwunderlich, da das Agile Manifest Elemente aus “Lean” formuliert. Im folgenden Fallbeispiel ist ein Projektleitbild für ein Projekt zur deutschlandweiten Einführung eines Personalverwaltungssystems (PVS) dargestellt.
Erfolg im Team | Auftraggeber und Auftragnehmer streben gemeinsam als Team den Projekterfolg an. |
Erfolg für alle | Das Projekt ist dann erfolgreich, wenn das Ziel im Einklang von Qualität, Ressourceneinsatz und Termintreue erreicht wird. |
Erfolg durch Kommunikation | Die Projektteammitglieder betreiben eine (pro-) aktive, umfangreiche Kommunikation (und kein “aktives Warten”). Dazu gehört auch die frühzeitige Eskalation. |
Erfolg durch Führung | Die Projektleitung übt eindeutige Richtlinienkompetenz aus. |
Erfolg durch Vertrauen | Vor dem Vertrag steht die gemeinsame Lösungsfindung. Vertragsdiskussionen nicht im Tagesgeschäft. |
Erfolg durch Erfahrung | Das System PVS ist erst am Ende von Roll-out 2 abgeschlossen. |
Siehe dazu auch Lean Project Management: Verschwendungsarten in Projekten und Unternehmenskultur und Projektkultur im Spannungsfeld zwischen “Tight” und “Loose”.

Solche Zusammenhänge thematisieren wir auch in den von uns entwickelten Blended Learning Lehrgängen Projektmanager/in (IHK) und Projektmanager/in Agil (IHK), die wir an verschiedenen Standorten anbieten. Weitere Informationen zu den Lehrgängen und zu Terminen finden Sie auf unserer Lernplattform.